EPR Compliance in Oregon for SMBs
Oregon’s EPR rules affect SMBs. Learn about producer types, packaging data, and key deadlines for compliance by March 31, 2025.
With Extended Producer Responsibility (EPR) regulations taking effect across the U.S., small and medium-sized businesses (SMBs) in the Consumer Packaged Goods (CPG) sector must navigate complex compliance requirements.
Oregon’s EPR law requires producers to manage and report packaging waste, with a key filing deadline of March 31, 2025. This guide simplifies the compliance process, helping businesses determine their obligations and reporting options.
Section One: Understanding Producer Classification
Oregon categorizes producers based on global gross revenue and total weight of covered materials sold in the state:
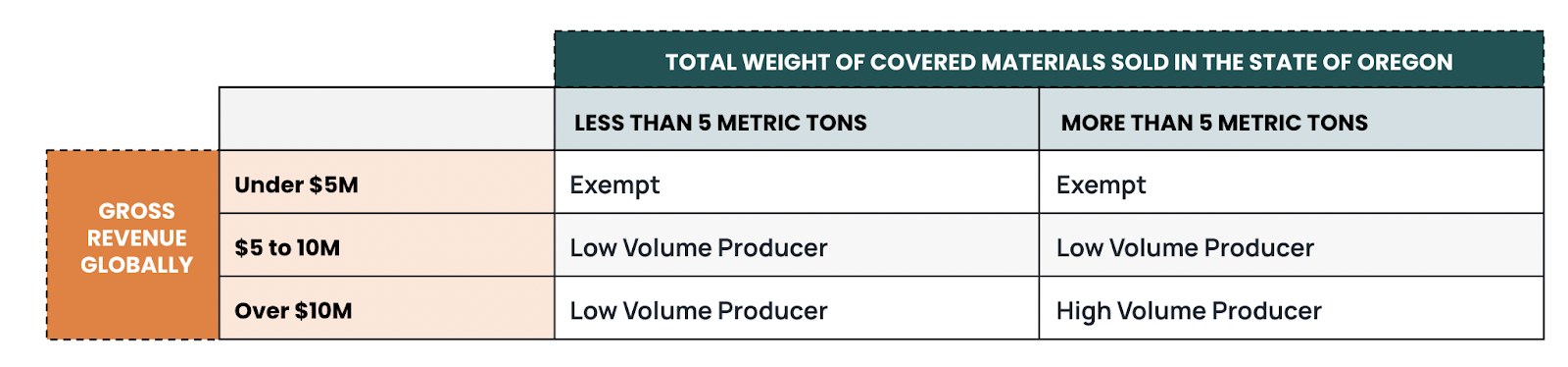
Exempt Producers: Small businesses with less than $5M in revenue and less than 5 metric tons of covered materials sold.
- Low-Volume Producers: Companies below the $10M revenue threshold or selling less than 5 metric tons.
- High-Volume Producers: Companies exceeding both $10M revenue and 5 metric tons of materials.
High-volume producers must submit detailed weight-based reports, while low-volume producers have simplified reporting options.
Section Two: Identifying the Best Reporting Option For You
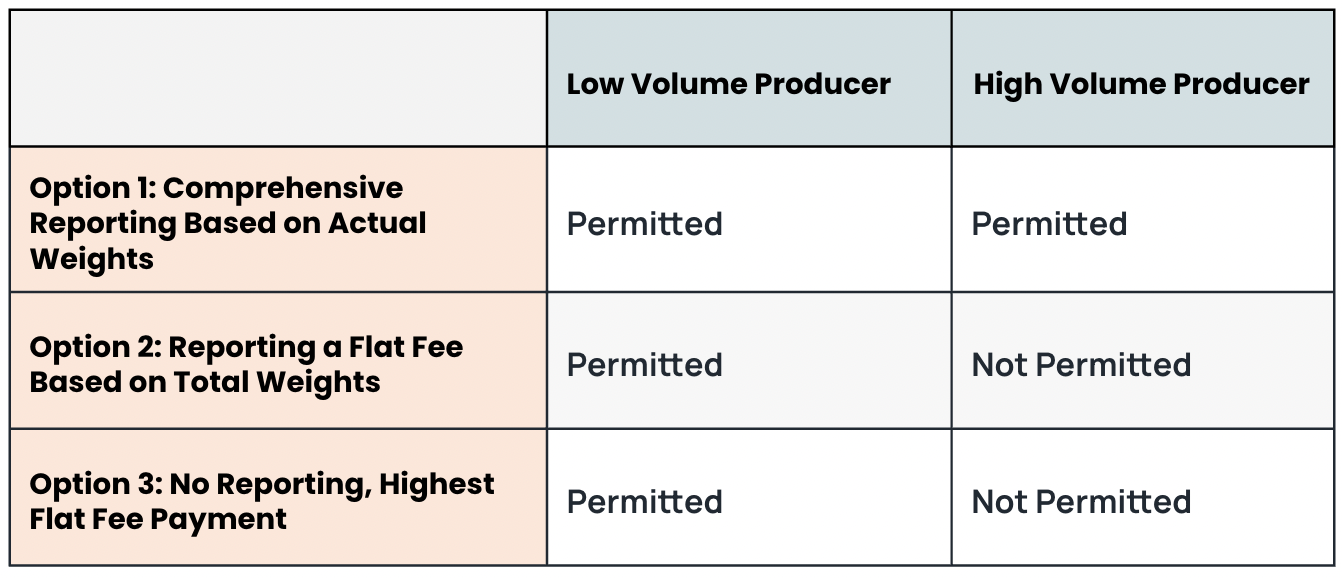
Three Reporting Options for Low-Volume Producers
Oregon offers three ways for low-volume producers to comply:
1. Comprehensive Reporting (Most Accurate & Cost-Effective)
- Requires reporting actual packaging weights by material category.
- Ensures precise fee calculation and potential cost savings.
- Best for brands planning to scale beyond $10M in revenue.
Steps to Comply:
- Identify all affiliates, brands, and subsidiaries.
- Use an approved methodology (SMRM, ABOM) to calculate packaging weights.
- Categorize and report total material weight to the Circular Action Alliance (CAA).
2. Flat Fee Reporting (Simpler, but Less Optimized)
- Companies report total packaging weight without material breakdown.
- Fees are tiered based on total estimated weight.
- Easier administration, but potentially higher costs than weight-based reporting.
Steps to Comply:
- Identify all affiliates and subsidiaries.
- Estimate total packaging weight using accepted methodologies.
- Submit data and pay the applicable flat fee.
3. No Reporting, Highest Flat Fee (Costliest & Least Flexible)
- Producers can skip reporting altogether by paying the highest applicable flat fee.
- Eliminates data collection but often results in overpayment.
Who Chooses This?
- Companies struggling with packaging data collection.
- Brands seeking the simplest but most expensive compliance route.
Reporting for High-Volume Producers
Companies that exceed $10M in revenue and 5 metric tons must complete a detailed reporting process:
- Calculate Supply Volumes – Track sales and packaging weight data.
- Use Accepted Weight Calculation Methods – SMRM (preferred), ABOM, or sector calculators.
- Categorize & Report Data – Submit material-specific weights to CAA.
This data-intensive process ensures compliance but requires robust tracking systems.
Why Specific Material Reporting (SMRM) is the Best Choice
rePurpose Global encourages producers to adopt the Specific Material Reporting Method (SMRM), which:
✔ Ensures accurate fee calculations (no overpayments).
✔ Aligns with future EPR regulations across other states.
✔ Helps brands qualify for eco-modulated incentives (lower fees for sustainable materials).
✔ Enhances supply chain transparency and sustainability insights.
While ABOM (Average Bill of Materials) offers an estimated approach, it lacks precision and may result in higher costs over time.
Key Deadlines & Compliance Checklist
📅 March 31, 2025 – First Oregon EPR report due.
📌 What You Need to Do Now:
☑ Determine your producer classification.
☑ Choose a reporting method.
☑ Gather sales and packaging weight data.
☑ Submit reports via the CAA Producer Portal.
Check out our ultimate guide to Oregon EPR compliance, made for small and medium businesses.
How rePurpose Global Can Help
Navigating EPR regulations can be challenging, but rePurpose Global offers a packaging compliance software platform that simplifies reporting and ensures cost-efficient compliance. Our tools help brands:
✔ Automate packaging weight tracking.
✔ Ensure accurate fee calculations.
✔ Stay ahead of regulatory changes.
Take action today to avoid last-minute compliance stress!
Check out the EPR packaging module.
Get Started with Verified Plastic Recovery for your Brand
Get Started with Packaging EPR Compliance for your Brand
rePurpose Global is here to support your sustainability roadmap with impactful and measurable Plastic Action solutions that deliver immediate results. Partner with us to measure your plastic footprint, fund plastic waste recovery, and create strong sustainability messaging for your brand.
Talk to our team to explore how we can work together.
rePurpose Global's EPR compliance platform is here to support you in preparing for the upcoming regulations in multiple states in the US and comply with no errors. Partner with us to create detailed assessment reports, pre-empt fees and reduce time & cost involved in the process.
Talk to our team to explore how we can work together.
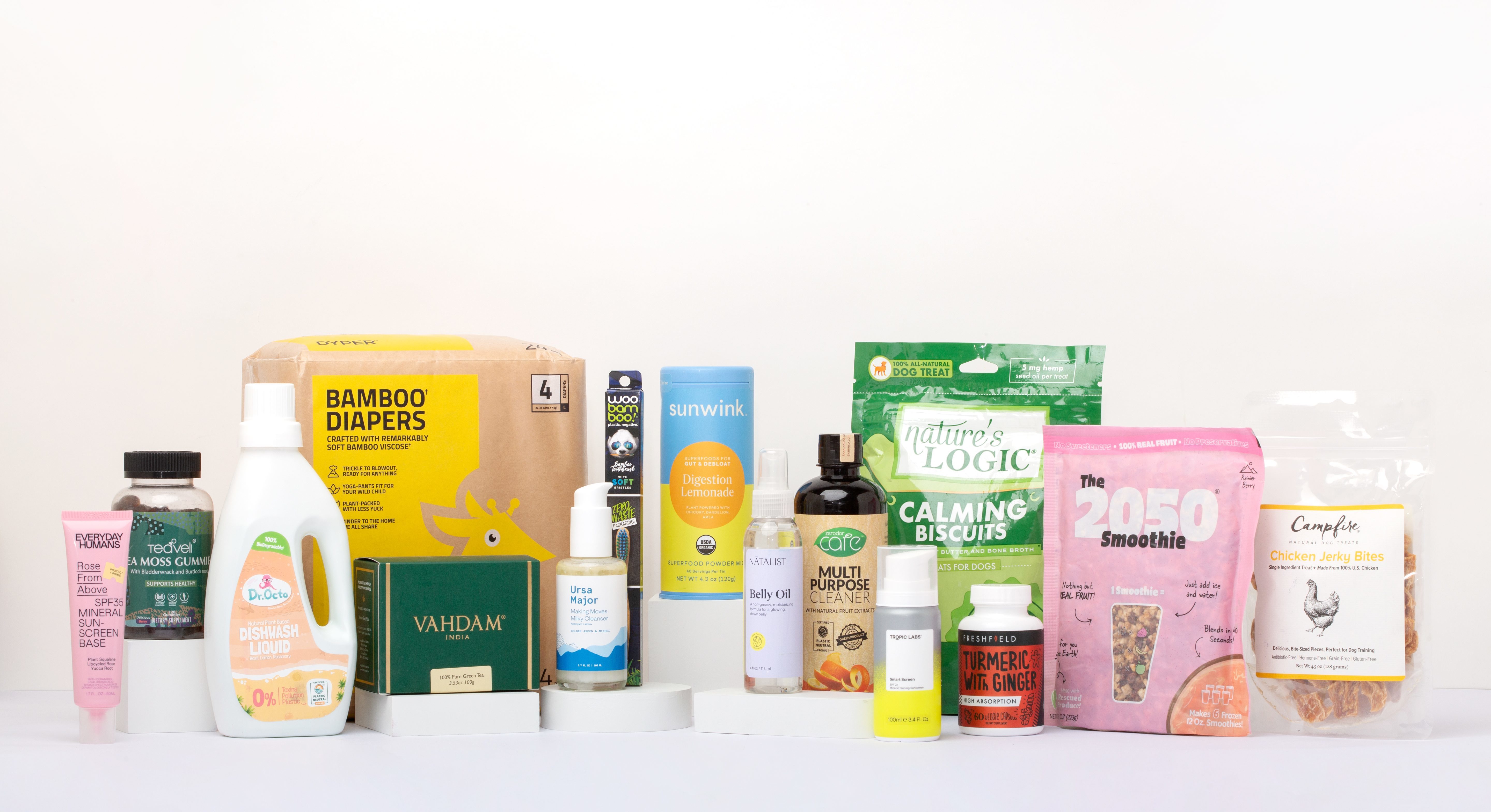
Related Posts
EPR Foundations: What does Cost Coverage mean?
Learn how EPR laws shift recycling costs to producers and incentivize sustainable design through fees and program funding.
EPR Foundations: What is the Circular Action Alliance?
Learn how Circular Action Alliance helps brands meet EPR goals with streamlined reporting, cost savings, and policy alignment.
EPR Foundations: What is a Producer Responsibility Organization?
Learn how PROs like Circular Action Alliance help brands comply with EPR laws while reducing costs and simplifying reporting.